浓盐水处理前:Q =13~23t/h,平均流量Q =18t/h。盐含量浓度约为10-15%,其中氯化钠约70~90%,氯化钾约10~30%,盐水pH值7.5~10,温度60~80℃。盐水中悬浮物约1000~3000mg/L。盐水中含有氨的存在,氨氮总含量正常状态约0.2%,蕞高不超过1%。盐水中存在氟离子,氟离子浓度100~500mg/L,极端情况下氟离子浓度约1000mg/L。
浓盐水处理后:盐水中悬浮物约<100mg/L,钙离子浓度<50mg/L,镁离子浓度<50mg/L,氟离子浓度<20mg/L,pH值>10。
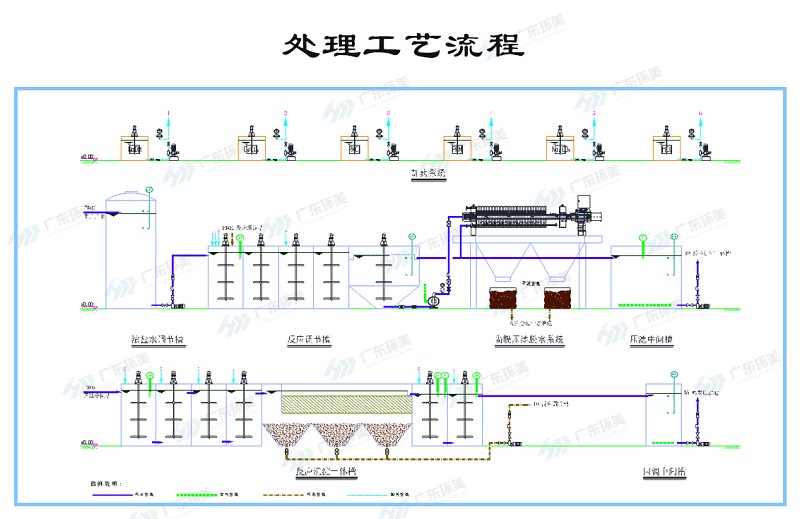
为了能更髙效的去除高盐废水中的钙镁离子及氟离子,设计采用两级物化处理工艺,其中一极物化处理系统主要用于镁及氟的去除,二级物化处理主要针对钙的去除以及氟的进一步去除,具体处理工艺流程如下:
(1)生产产生的高盐废水,经收集后自流至高盐废水调节池,高盐废水经调节池充分均质均量后,可保障废水处理系统的稳定运行;
(2)高盐废水经充分均质均量后,废水经泵提升进入一极物化处理系统,一极物化系统主要由一极反应槽、一极沉淀槽、压滤机及压滤水槽组成,废水经泵提升后首先 进入一极反应槽,通过加药系统往一极反应槽内投加液碱、氯化钙、PAC及PAM,此时废水中绝大多数镁离子形成氢氧化镁沉淀物从而被分离,废水中大部分氟离子形成了氟化钙沉淀物而被去除,反应所形成的细小悬浮物,经PAC与PAM反应作用后,细小悬浮物或胶体微粒互相吸附结合而成较大颗粒,并使得悬浮物从水中迅速分离,废水经一极反应后,进入沉淀槽,如果当废水反应形成的悬浮物量不大,不影响沉淀槽的正常固液分离时,废水经沉淀槽固液分离后,污泥进入压滤机进行脱水,压滤机产生的泥饼委外处置,压滤机产生的滤液自流进入压滤水槽,沉淀槽清液则直接进入压滤水槽;如果当废水反应形成的悬浮物量很大,影响了沉淀槽的固液分离,沉淀槽中的泥水混合则通过泵全部提升至压滤机进行固液分离,压滤机产生的泥饼委外处置,压滤机产生的滤液自流进入压滤水槽。
(3)压滤水槽中的废水经泵提升后,进入二级物化处理系统,二级物化处理系统主要由二级反应槽、二级沉淀槽、pH调节槽及中间水槽组成,废水经泵提升后首先 进入二级反应槽,通过加药系统往而级反应槽内投加盐酸、碳酸钠、PAC及PAM,此时废水中溶解的部分铝盐形成氢氧化铝沉淀物从而被分离,废水中的钙离子形成了碳酸沉淀物而被去除,反应所形成的细小悬浮物,经PAC与PAM反应作用后,细小悬浮物或胶体微粒互相吸附结合而成较大颗粒,并使得悬浮物从水中迅速分离,另外氟离子与PAC结合被进一步去除,为保证反应效果,反应pH控制在7-9,经反应后,废水进入二级沉淀槽,废水经二级沉淀槽固液分离后,污泥通过泵提升至一极反应槽,沉淀槽清液则直接进入pH调节槽,为了去除过量的碳酸盐,防止后端蒸发系统浓缩结垢,pH槽首先调节pH至4.0左右,充分去除水中的碳酸盐,同时为了蕞大限度的去除氟离子对蒸发的影响,调节槽内投加片碱,将废水pH调整至10以上,回调后的废水随后进入中间水槽,蕞后通过提升泵提升至蒸发原水池。
(1)浓盐水:浓盐水进料量13t/h,厂家考虑10%循环料量;盐含量浓度约为10-15%,其中氯化钠约70~90%,氯化钾约10~30%,盐水pH≥10,温度60~80℃。盐水中含有氨的存在,氨氮总含量正常状态约0.2%,蕞高不超过1%。盐水中存在氟离子,F-含量不超过30mg/L,盐水中存在氟、钙、镁离子,F、Ca、Mg含量不超过100mg/L。要求蒸发器蒸发量15t/h。
(2)硫酸铵溶液:间断进料量1t/h,浓度30%(wt),PH值5~6,常温。要求蒸发器蒸发量1t/h。
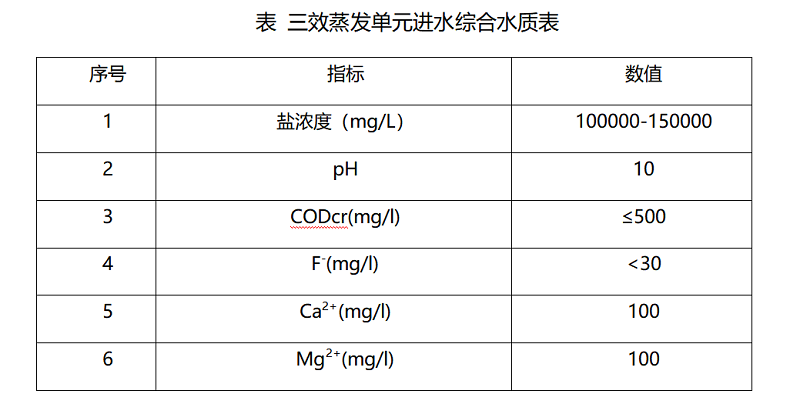
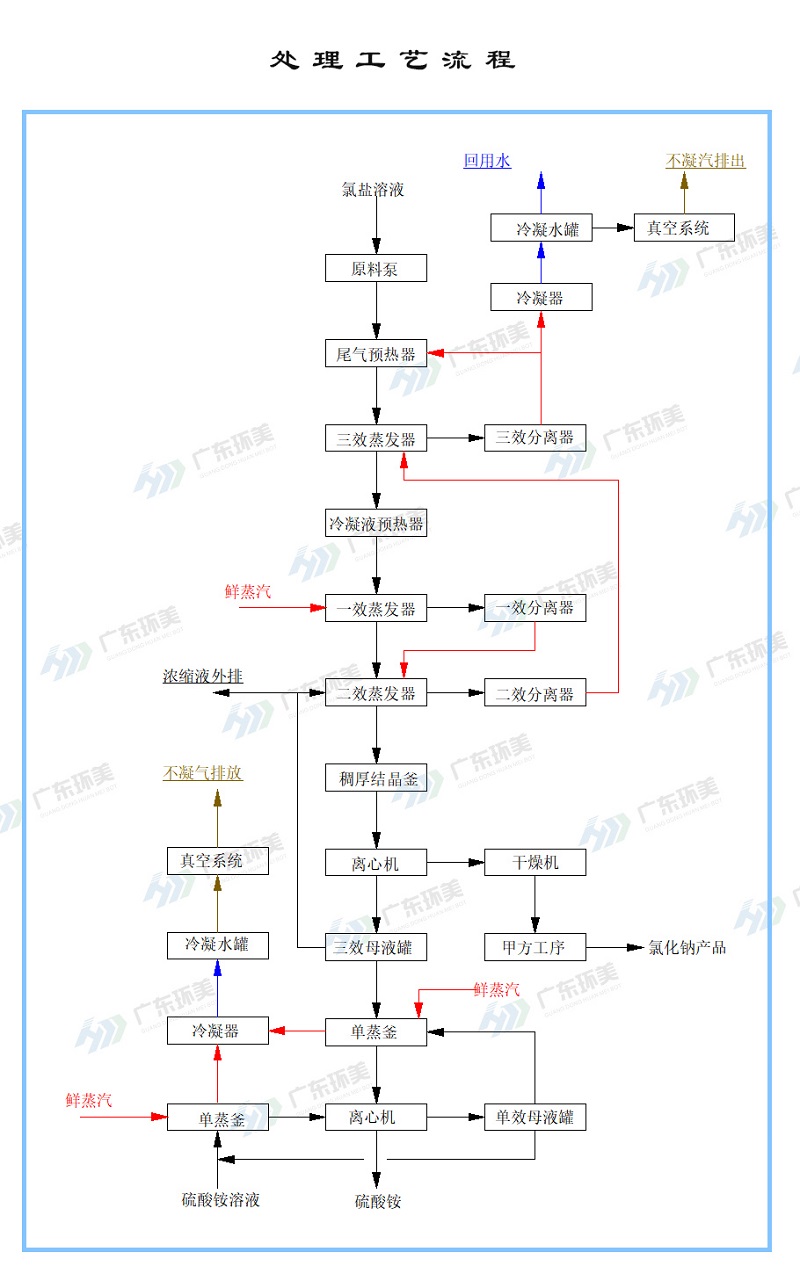